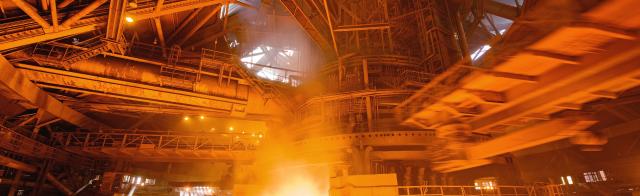
CHALLENGE
Sintering facilitates feed of iron ore fines in blast furnace, blended with fluxes and coking coal / coke. The depletion of iron ore quality poses new challenges to steel makers. There is a need to find alternate solutions maintaining optimal composition and metallurgical properties of the sinter to enable the production of high-quality hot metal and finally steel.
It is well established that lime has positive effects on the productivity of the sintering process and fuel savings. Lime, as an intensifier of the sintering process, leads to improved agglomeration and permeability of the sinter mix. Lime addition into sinter mix indicates a positive effect on the heat content in the sinter bed leading to shortening sintering time and possible fuel savings. Based on experimental results, partial usage of lime in the sinter mix brings also a positive environmental influence.
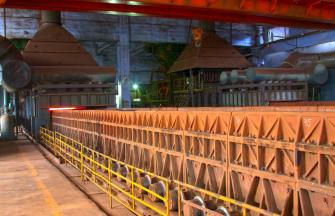
SOLUTION
Burnt lime, as compared to limestone, improves the heat transfer in the sintered layer. At the same basicity and the same volume of fuel, a change in the CO2/CO ratio can occur, due to the different amounts of carbonates after their replacement by lime. For lime too, the quality, granulometry, quantity, and method of lime addition to the agglomeration process are critical to sinter performance and productivity.
The granulometry is important for the creation of uniform blending, which influences the permeability of the charge, and hence the associated burning and heat transfer conditions during sintering. A controlled and engineering lime dosing during agglomeration could potentially increase the sinter productivity by about 20%, reducing the cost per ton, and the return sinter.
Carmeuse research on lime characteristics for sinter enabled Carmeuse to offer engineered products and customized services for improving quality of the sinter, keeping focus on cost savings and reducing environmental impact of the sintering process.
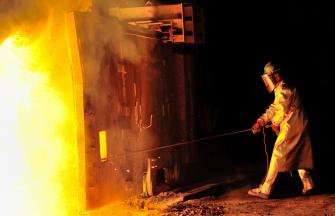
EXPERTISE
Carmeuse is constantly working to enhance knowledge in products and processes in order to satisfy individual application needs of the steel industry. We developed expertise in offering customized solutions (screened lime, high surface lime, fine lime, milled lime, delayed reactivity lime and hydrated lime) based on numerous sets of experiments related to the sintering process.
We at Carmeuse developed expertise in offering customized solutions based on numerous sets of experiments related to the sintering process. Sintering of iron ore has always been a potential process to improve emissions and reduce cost. Carmeuse research on lime characteristics for sinter enabled to offer engineered products and customized services for improving quality of the sinter, keeping focus on cost savings and reducing environmental impact of the sintering process.
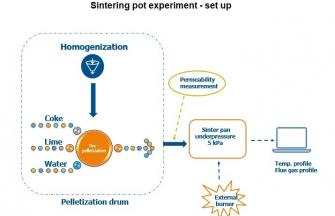