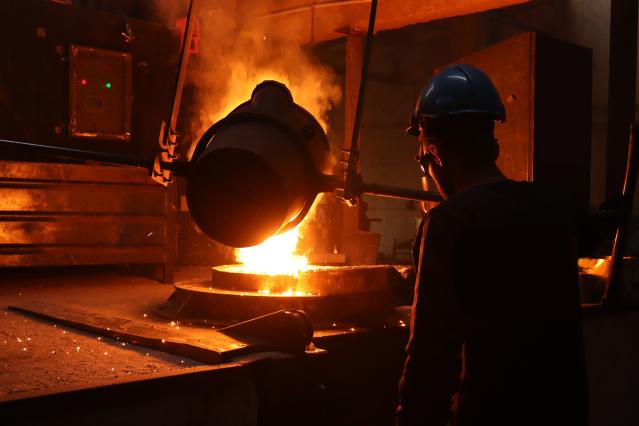
Do you have a question about this product? Ask our specialists
Contact us
Your Benefits
INDUSTRIES
- ON TIME IN FULL (OTIF): delivered on time in quality and quantity
- Security of supply: secured and reserved capacity
- Total Cost of Ownership (TCO) Reduction: supporting optimal use of the product
CUSTOMER INTELLIGENCE
- Product quality: the best suiting product for your need
- Value-added products
- Independence from the raw material availability
PARTNERSHIP
- Secured supply
- Long-term contract
- High value in use
More Information
Secondary steelmaking slag is in liquid form in the ladle and floats on the surface of liquid steel, which is usually at temperature of 1,600 degrees or higher. It acts like a sponge to absorb the impurities consisting mainly of sulphur and non-metallic inclusions. The design of the slag is a critical step impacting the efficiency of the steel refining processes during the secondary steelmaking.
Synthetic slags to adapt the slag composition are then greatly influencing deoxidation and desulphurization of the steel, while not affecting the ladle refractories. In addition, it allows to cover efficiently the steel to prevent heat loss by radiation and reoxidation from the atmospheric oxygen, and reduces dust float pollution.
Synthetic slags by Carmeuse are prepared with a special and customized design in terms of chemical composition, fusing capacities, and liquidus state at proper temperature. It typically contains CaO and MgO provided by high quality quicklime and aluminium-based compounds.
Handling is also important to prevent losses, and products are typically offered in the form of lost packaging bags to be dropped into the ladle or in the form of briquettes.
Process step | Critical parameters | Typical consumption (kg/ton of steel) |
---|---|---|
Secondary Metallurgy: Ladle Furnace | 1. Quality level and consistency 2. Tempered reactivity 3. MgO level | Synthetic slag 3-20 |
Secondary metallurgy challenges are pretty dependent on the efficiency of the primary steelmaking. It is also pretty different from EAF route compared to BOF route, which may or may not contain an efficient desulphurization step. The level of oxidation in the slag will also depend on the treatments that have been needed before. Evaluating both chemical and deoxidation needs, without forgetting the fluxing capability, is a necessity to get the most adapted product for efficient and cost-effective refining.
CaO in lime is essential to balance the basicity and contributes efficiently to the desulphurization in good oxidation conditions. Dolime will also bring some MgO to prevent it from reacting with the refractory of the ladle. Lime reactivity also plays an essential role in getting rapidly the needed activity in the slag. High lime purity is also required to avoid any pollution in the steel, notably of course sulphur and silica, but also for example the CO2, that will be influencing negatively the alloying.