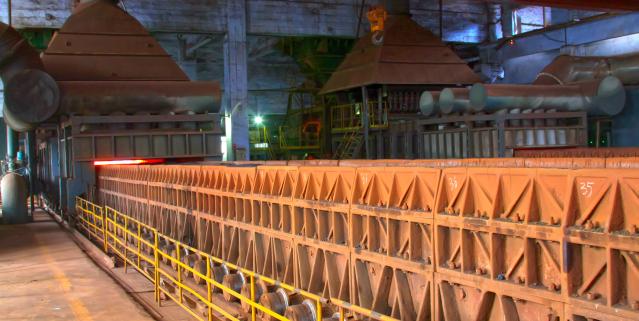
Do you have a question about this application? Ask our specialists
Contact us
Features & Benefits
Features
- Partial replacement of limestone with high quality lime and proper addition moment will lead to a stable quality and basicity of sinter.
- Lower content of impurities and higher CaO conduct to a better basicity of final product in sinter plant.
- Burnt lime, as compared to limestone, improves the heat transfer in the sintered layer.
- The quality, granulometry, quantity, and method of lime addition to the agglomeration and sintering process are critical to four aspects of the plant: sintering performance, productivity, fuel rate, and environmental footprint.
- Increasing basicity is beneficial to the coalescence behaviour of the sintering process and makes the densification coefficient increase.
- Online measurement of sinter mix chemical composition allows to monitor lime addition and adjust basicity index.
Benefits
- The amount, type and quality of fluxes have a significant role in deciding sinter quality, potentially resulting in improved energy usage and lower emissions from the ironmaking processes. High sinter basicity index increases sinter productivity.
- Partial replacement of limestone with lime leads to a very significant sintering process productivity increase.
- At the same basicity and the same volume of fuel, a change in the CO2/CO ratio can occur, due to the different amounts of carbonates after their replacement by lime.
- A balanced sinter quality and high basicity meet blast furnace specifications.
- Monitored addition of lime allows to adjust the basicity index with better constancy.
Dedicated solutions for your specific needs
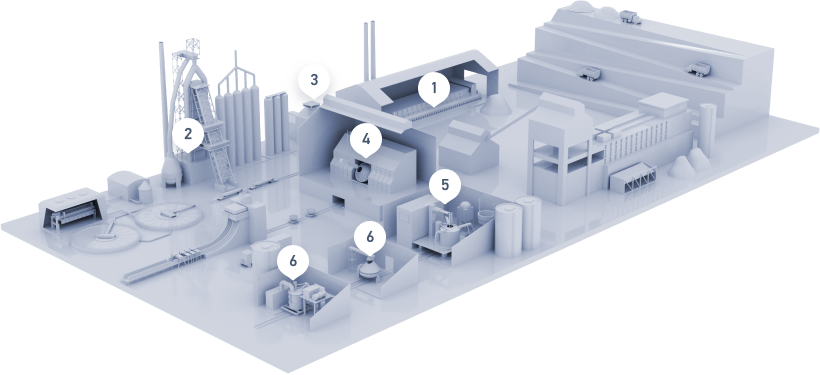
More information
The metallurgical properties of iron ore sinter mainly depend on sinter mineralogy and microstructure, which in turn depends on the chemical composition of the sinter mix. In order to meet blast furnace requirement on sinter quality, it is essential to optimize the CaO and MgO in sinter mix and sinter basicity to get desired properties.