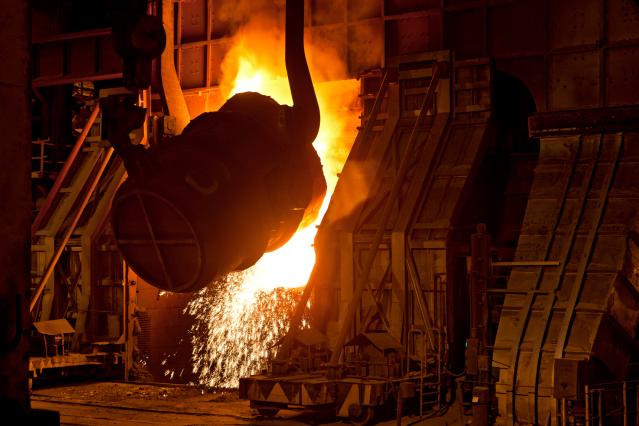
Do you have a question about this product? Ask our specialists
Contact us
Your Benefits
INDUSTRIES
- ON TIME IN FULL (OTIF): delivered on time in quality and quantity
- Security of supply: secured and reserved capacity
- Total Cost of Ownership (TCO) Reduction: supporting optimal use of the product
CUSTOMER INTELLIGENCE
- Product quality: the best suiting product for your need
- Value-added products
- Independence from the raw material availability
PARTNERSHIP
- Secured supply
- Long-term contract
- High value in use
More Information
The metallurgical properties of iron ore sinter mainly depend on sinter mineralogy and microstructure, which in turn depends on the chemical composition of the sinter mix. In order to meet blast furnace requirement on sinter quality, it is essential to optimize the CaO and MgO in sinter mix and sinter basicity to get desired properties. Engineered fine lime with proper grain size and reactivity is offered to get the best performing agglomeration and sintering efficiency with reduced fuel consumption and improved yield.
Process step | Critical parameters | Typical consumption (kg/ton of steel) |
---|---|---|
Sinter plant | 1. Quality level and consistency 2. Tempered reactivity 3. MgO level | Milled Quicklime 0-25 |
Hot Metal Desulphurization | 1. Quality level and consistency 2. Impurities (S) 3. High flowability for injection | Milled Quicklime 5-10 |
Quicklime on the contrary to calcium carbonate, is already in the form of oxide and it doesn’t require additional energy to decarbonize. In addition, quicklime has flocculating properties that help agglomeration and resulting permeability of the mix.
Although magnesium metal is the main material used today for hot metal desulphurization, lime has also a high desulphurization capacity, which is enhanced together with magnesium. To have a deep injection in the hot metal with dense phase transport and effective reaction yield with low iron droplets moving to the slag, a high specific surface and flowability is required.