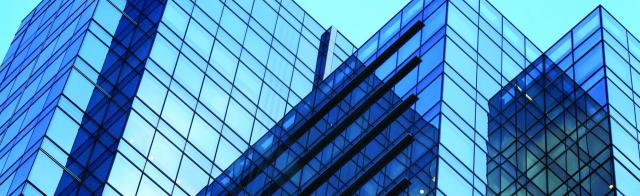
GLASSMAKING: A BRIEF INTRODUCTION
Glass is a ubiquitous material in the modern world. It comes in many types and with many uses: from lead glass, used (among other things) to make crystal tableware; to borosilicate glass, used in cookware and laboratory glassware; and fiberglass—to name just a few. However, the most prevalent type of modern glass is soda-lime glass, which comprises about 90% of glassmaking and is the focus of this article.
Soda-lime glass is used to produce both flat glass for windows, automobile windshields and architectural purposes and container glass for food, drink and other commodities. As its name suggests, it is made using a basic mix, or batch, of three primary raw materials. Silica (silicon dioxide, SiO2)—the basic ingredient of almost all glasses—accounts for 70% to 75% of the batch; soda (sodium oxide, Na2O) about 15%; and lime (calcium oxide, CaO) about 10%. These percentages are industry benchmarks, but can vary slightly based on factors, such as manufacturing process and desired end product. In addition, a batch may contain cullet (crushed rejected or recycled glass). The lime is generally added to the batch in the form of limestone (calcium carbonate, CaCO3), which decomposes to lime in the glass furnace, releasing carbon dioxide (CO2).
Although the raw ingredients are relatively simple, their proper selection is crucial. When it comes to limestone, the chemistry, sizing, moisture and impurities all impact the glassmaking process in a range of ways that will be discussed later. We start, however, with a more detailed look at the limestone itself: how and why it is used, and the different types that are available.
WHY LIMESTONE?
Basically, there are increased processing costs for producing lime from raw limestone. So typically, limestone is chosen for lower cost, but also because over time glass manufacturers have become accustomed to using limestone which has proven to meet high quality standards. Each of the three components mentioned above has its own particular purpose in the glassmaking process. Silica—when melted—forms the glass, but its melting temperature is very high, often in excess of 3110°F (>1710°C), and this makes handling the glass difficult. Soda is therefore added as a flux to reduce the melting temperature, but it also weakens the glass and makes it soluble in water. Limestone stabilizes the glass, solving the issue of solubility and increases its hardness and chemical durability.
However, the benefits of limestone are broader than this brief outline suggests. It also plays a role in lowering the melting temperature of the batch by improving the melting kinetics. As a result, the various ingredients of the batch melt congruently and at a lower temperature than the individual melting temperatures of each of the constituent parts (a property known as an eutectic mixture). This means less energy is consumed by the melting process, reducing costs, and providing environmental benefits.
Limestone also helps to improve the handling and formability of the molten glass. In a pure silica melt, viscosity is high and this (alongside with high temperature) makes the glass difficult to shape, especially when it needs to hold a form, for example, in the production of glass containers. Limestone reduces the viscosity, making the liquid glass easier to handle and form into the required shape.
A final benefit of limestone in glassmaking is that it helps to avoid devitrification, a process of crystallization around small impurities in the mix that causes clouding and other defects.
TYPES OF LIMESTONE
Limestone is therefore an essential part of the batch. However, limestone comes in two basic types: high calcium and dolomitic. The difference between the two relates to the relative magnesium (Mg) content. High-calcium limestone is almost entirely CaCO3 with 1%—3% impurities. Dolomitic limestone contains about 35% to 45% magnesium carbonate (MgCO3); the remainder is primarily CaCO3, again with 1%—3% impurities.
The balance of calcium and magnesium content effects the glassmaking process in a number of ways. For example, it affects the viscosity at different temperatures by adjusting the steepness of the viscosity curve. How do you determine which of these two types of limestone is going to work best in your process?
Flat glass manufacturers tend to use more dolomitic limestone, since the higher magnesium content helps to counteract crystallization in the tin bath during cooling, which is slower than in container glassmaking. It also helps to avoid ‘hazing’ after the tin bath. Too much calcium in the batch creates a calcium-rich surface at the end of the bath that attracts water vapor and carbon dioxide, creating a white film on the surface of the glass. Although acid can be used to remove this film, from a health, safety and environmental perspective—as well as a cost and process optimization basis—it is better to avoid its formation in the first place.
If you are a container glass manufacturer, high-calcium limestone may be more appropriate, as the glass is cooled more rapidly than in flat glass production, so that it keeps its form during the blowing process. Faster cooling presents less of a risk of devitrification and is less sensitive to hazing.
Fiberglass manufacturers tend to use more dolomitic limestone. However, the choice of limestone is highly dependent on the desired properties of the fibers, which vary widely depending on the type of fiberglass being produced. Carmeuse application specialists can provide more information on the best use of limestone in fiberglass production, tailored to your process.
Ultimately, however, whichever limestone you are using in your process, the important characteristics are consistency of chemistry and sizing.
CONSISTENCY IS KEY
The basic chemistry of limestone comprises calcium, magnesium, iron and silica. Of these, calcium and silica are essential for glassmaking, as has been discussed previously, although most of the silica in the batch comes from silica sand. Magnesium also has its benefits, again as outlined above. Iron—the primary impurity in limestone from a glassmaking perspective—is often the driving factor in the specification of limestone chemistry, as it colors the glass. This can be beneficial, for example, when making tinted flat glass or amber and flint container glass. However, glass makers should be aware of the potential impact of iron on their particular process when specifying limestone.
When it comes to chemistry, the parameters will be determined by the application and desired properties of your final product, since different types of glass have a different range of chemistries. Carmeuse application specialists will be able to help you specify the most appropriate limestone for your particular process.
When it comes to sizing of the limestone, homogeneity is key. The presence of too large a particle size (6-mesh/2-3mm) is undesirable as it will increase the melt time and risk the inclusion of solid particles in the glass after melting. In addition, little eutectic liquid will be formed because there is less particle interaction.
On the flip side, the presence of too many fine particles (<70-80 mesh/200µm) can make it harder to control the speed of the melt. Melt too quickly, and the carbon dioxide produced as the limestone decomposes into lime will not be able to leave the liquid, causing gaseous inclusions (bubbles) in the final product. Fine limestone particles can also result in dusting in the work area, presenting a health and safety challenge.
A final aspect of limestone composition is the moisture content, where typically you are looking for about 5% moisture. This tends to be the natural amount that helps to control dust and segregation without unduly influencing the process. More moisture is also added to the batch—in the form of steam—for compaction just before it is pushed into the furnace.
LOOKING TO THE FUTURE
The glass industry is constantly coming up with new and innovative advancements that includes both products and manufacturing processes.
Products like solar panels, recycled glass, smart glass, filtering systems for environmental sustainability, and a wide variety of glass use in electronics, including fiber optics for high-speed communications, will require adaptation of raw materials to meet these new demands.
Contemporary manufacturing technologies centered around energy efficient electrical furnaces, improved energy consumption, reduced emissions, and national energy security will certainly dictate how reagents impact production processes.
At Carmeuse, we listen to the market needs to evaluate and prepare for the continued use of limestone as an essential component in the industry’s advancements.
HOW CAN CARMEUSE HELP?
As a leading expert in the manufacture and use of lime and limestone products, Carmeuse is well positioned to be your partner to supply and optimize the use of limestone in your glassmaking process. At our plants, we produce the consistency of material that you need, while our distribution network ensures a reliable supply.
We are also supported by the expertise of a team of customer applications specialists based out of the Carmeuse Innovation Center in Pittsburgh. These experienced professionals are available to answer any questions you may have about our limestone, how it relates to your specifications, and its optimal use in your process. Our goal is to make sure you are asking for and receiving the right product for your application.
Click here to download the article.