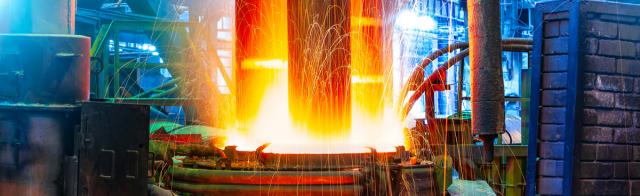
The Benefits of Lime Injection in the Electric Arc Furnace
Lime use as a fluxing agent in steelmaking is well documented. In recent years, injection of lime has also shown to be a viable technology that benefits the steel-making process. Injection of lime and dolomitic lime throughout the melting process, rather than adding late in the heat, has led to significant energy savings and improved slag chemistry. In addition, better utilization yield of lime, reduced fines emission and enhanced safety are achieved by the lime injection technology.
A BETTER WAY TO ADD LIME
Historically, steelmakers have experimented with various methods for adding lime to the EAF including scrap bucket discharge, fifth-hole addition through the roof, super sack drops and lime screening and briquetting.
However, many of these techniques created significant environmental issues with lime emissions in the shop. Even with some improvement in reducing lime emissions using the fifth-hole through the roof, lime fines were still generated through the various drop points and transferred to the baghouse through the furnace evacuation system. The impact from these mechanical systems could be seen in lime yield being lost to the baghouse and in the shop environment.
The emergence of the foamy slag practice to protect the furnace sidewall and refractory created a need to efficiently introduce lime during the melting process. It is highly desirable that lime is added to the process at the right time and in the right position within the furnace. Early attempts at sidewall lime injection were made in the early 1990s. Since then, advances have been made in areas of equipment design, slag practice and lime quality.
Lime injection now provides a reliable technology for steelmakers to control foamy slag, reduce waste disposal, improve safety and save electrical energy.
DENSE VS. DILUTE PHASE
The pneumatic conveying of material has created some confusion among steelmakers as to whether they should use dense phase or dilute phase for material transport through the injection system.
In dilute phase mode, materials are conveyed with a large volume of low-pressure air. Particles in the pipe are suspended in the fast moving air at velocities above what is called the saltation velocity. This is the point at which particles will drop out of suspension in the air stream and begin bouncing along the bottom of the pipe.
In dense phase mode, materials are conveyed with a lower volume of high-pressure air producing a velocity that is below the saltation velocity. This creates individual plugs which are moved by boosts of compressed air.
The optimum method for lime injection is dense phase. This allows fine particles of lime to be injected into the EAF through the injection lance, which is located close to the slag for deeper penetration into the slag and metal interface.
Lime injection results in faster dissolution of lime because of the larger surface area afforded by smaller particles injected directly at the slag and metal interface.
It improves lime yield and slag chemistry control. In addition, steelmakers can realize simpler housekeeping efforts, improved environmental conditions and less mechanical repairs of conveyor systems.
Consistency and control are of paramount importance for lime injection. Key factors to consider are:
- Degradation and segregation of products from lime plant to steel plant
- Different flowability of the injection materials
- Distance from the day bin to the injector and distance from the silo to the day bin
- The number of bends in the lime delivery system
- Design of the feeding mechanical system and the path to the injector
- Variability of air pressures throughout the system
- Control feedback and instrumentation
These variables can present challenges to the consistent control of lime injection. However, they can be mitigated through proper planning and disciplined shop practices.
To download a PDF of this article, please click here.
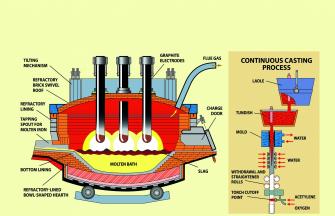
FLOWABILITY
It is well understood that lime is friable, and it is not uncommon to have sizing variability from truckload to truckload. Product degradation and segregation during mechanical handling can cause this variability. This is especially true for dolomitic lime due to its softer nature compared to high-calcium lime.
Steelmakers are used to dealing with various-sized materials for injection, including high-calcium lime and dolomitic lime. The dispensing equipment is flexible for delivery of various materials to the injectors. Flowability issues with dolomitic lime from day bins to dispenses and finally to the injectors can be related to how the material reacts in a gravity flow process compared to an aerated process.
Consistency of flowability for lime can be of concern because of the following reasons:
- Mechanical size degradation with subsequent handling to the injection system
- Improper design of lime injection systems
- Segregation of the product in transfer from silos to trucks and back to silos
- Variability in lime properties related to particle shape, particle attraction and size distribution
There is no advantage in specifying size gradations since lime degradation from the original desired sizing can occur due to the mechanical handling during load out at the lime plant, transporting the lime, filling the silo at the steel plant and subsequent charging of the dispenser for injection.
In the case of dolomitic lime, fine particles tend to adhere to each other due to surface electrical charges and can influence flowability depending on the distribution of particle sizing.
Carmeuse has developed flow aids that can even out the difference seen in lime flow characteristics. This allows for improved control of flow to the lime injector and consistency in operation. The lime used for injection should yield satisfactory flow characteristics in transfer from truck to silo, in gravity feed from silo to the receiving hopper and in aerated conveyance from the hopper to the injector in the EAF. Overall, our work in the laboratory and in the field has advanced knowledge and improved the application of fine lime injection in the EAF.
LIME BENEFITS ARE REAL
Lime injection technology results in many benefits for steelmakers and is now proven as a viable tool for EAF operations. The growth of sidewall injection has expanded the possibilities for the injection of various materials that can provide cost-effective operations.
The efficient use of lime and better control of slag chemistry have led to significant energy savings for steelmakers.
Additional benefits include cleaner environments for shops, reduced volumes in lime-to-furnace evacuation systems, better lime yield resulting in less quicklime used during the melting process, and reduced main-tenance cost compared to mechanical systems.
In addition, improved injection technology means 100 percent injection of lime requirements for the EAF, faster dissolution of lime related to increased surface area of lime particles, flexibility in controlling slag characteristics throughout the heat, and improved steel process performance.
Please click here to download the article.