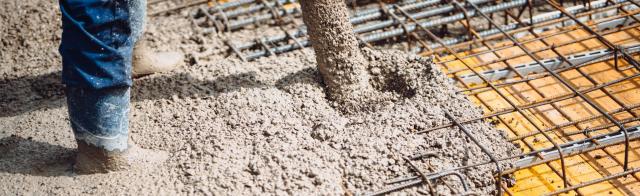
Consistent production. In the minimum time. At the lowest cost.
As a producer of self-consolidating or precast concrete, that is your mantra. It’s your business. Central to that is your concrete mix. You need the right balance of flowability, workability, durability, uniformity, and speed of curing—and you need it with every single batch. PREMIACAL enhanced concrete will help you consistently achieve this complex balance.
Introduced in North America at the 2009 National Precast Concrete Association’s Precast Show, PREMIACAL engineered milled limestone replaces a portion of the ordinary Portland cement (OPC) in your concrete mix and is designed to improve the look, workability, finishability, and durability of your concrete. Every time.
PREMIACAL should not be confused with traditional milled limestone
Milled limestone is, essentially, a fine calcium carbonate material that is produced by grinding limestone. Geologically and chemically, it’s not dissimilar to the limestone fines that are produced every day at quarries all over North America. Unlike typical limestone fines, however, PREMIACAL’s proprietary gradation is engineered to provide the purity, consistency, and particle size necessary to substantially increase the hydration reaction of cement.
Benefits of Using PREMIACAL
- Its ability to increase the hydration reaction allows for up to 15% replacement of OPC with PREMIACAL, reducing the cost of your mix.
- It has a considerably lower carbon footprint than OPC, helping to reduce the environmental impact of your operations.
- You can expect the same color, quality, and consistency to your end-product every time you add it to your concrete mix.
- It makes mix design a more predictable process and reduces the need for admixture adjustments.
- It is available whenever you need it. PREMIACAL is mined and milled 24/7, 365 days a year, at eight milled limestone plants in North America, so you do not need to worry about any disruption to supply.
This engineered consistency of PREMIACAL sets it apart from fly ash, the quality and availability of which continues to decline as North America transitions away from coal-fired power.
PREMIACAL also provides more flexibility and performs better than the pre-blended Type IL Portland-limestone cements produced by many cement companies. This is because cement companies are only concerned with blending to achieve a set percentage of limestone in their cement. This process leaves you without the ability to further vary the blend or obtain the full range of benefits PREMIACAL’s engineered particle distribution provides.
Producing your own blend of PREMIACAL and OPC, however, gives you full control of the mix to tailor to your unique needs. And thanks to its manufacturing process, PREMIACAL is a dry, free-flowing material, making it simple to store on site in a dry bulk silo and handle by pneumatic blower for a precisely controlled blend.
Added control and cost savings!
None of this means anything if it negatively impacts your bottom line. At the most basic level, PREMIACAL is a cheaper material than OPC. Using it in place of OPC in the concrete mix, therefore, reduces the cost of the concrete. It also avoids over-engineering the mix with 100% OPC in situations that do not require higher strengths. For example, a mix with 10% PREMIACAL may be required for a prestressed beam, but the portion could be increased to 15% for drainage pieces.
How does PREMIACAL work?
1. By replacing OPC with PREMIACAL engineered milled limestone in your mix, you will improve the particle size distribution within the concrete mix. This reduces segregation, surface bleed and surface imperfections during setting, as well as the permeability of the finished product, providing greater durability to freeze-thaw conditions, protecting against reinforcement corrosion, reducing alkali-silica reactions, and minimizing efflorescence.
2. The ultra-fine size of PREMIACAL is engineered to improve the flowability of the concrete, leading to faster and more complete filling of molds and around the reinforcement, and, therefore, minimizing voids (bugholes) or mis-formed casts. As a result, turnaround times are shortened, and production capacity can be optimized. It also makes it easier to pump and means less vibration or mechanical consolidation is required, saving on energy, equipment, and labor costs.
3. PREMIACAL speeds up the setting process—another key factor in turnaround times – while moderating the heat of hydration to prevent the faster hydration reaction from impacting the long-term performance of the concrete. To better understand this reaction, the fine limestone particles act as a nucleation site for hydration products, catalyzing their formation, particularly calcium silicate hydrates (C-S-H), and making sure they are homogenously dispersed. This can accelerate early strength, allowing you to remove forms faster.
4. Adding ground limestone to the cement mix is tried a tested solution. There are decades of research supporting the use of Portland-limestone cements by various organizations – from cement companies through to specifying agencies, owners and end users. It’s accepted in both US and Canadian standards, as well as in Europe, where PREMIACAL has been widely adopted.
5. In terms of applications, it’s consistency of color makes it a natural fit for any exterior or interior finishes—but when it comes to strength and durability, it can be used almost anywhere you would use OPC.
What about the environment?
So far, we have focused on the cost and performance benefits of PREMIACAL, but the environmental benefits are also significant.
OPC is the material in concrete with by far the largest carbon footprint. The cement industry as a whole is estimated to emit about 7% of global manmade CO2 emissions annually, and reducing the amount of OPC in concrete is widely recognized as a key pillar in limiting the environmental impact of concrete construction.
At the same time, at both national and corporate levels, there is an increasing emphasis on transparency in the reporting of actions taken to mitigate climate change. The sustainability advantage gained by using PREMIACAL to replace a portion of OPC in concrete is, therefore, likely to become an important consideration for construction companies and specifiers.
Limestone is a natural, abundant, and chemically stable product, that offers a significant reduction in CO2 production compared to OPC.
In conclusion, why PREMIACAL?
For a relatively simple product, the benefits gained by using PREMIACAL in self-consolidating and precast concrete production are numerous. It offers dependable quality, consistent color, and reliable availability. It lowers cost when replacing OPC, while maintaining durability and strength. It creates a concrete that is easier to pump and work, less prone to segregation, and quicker to set— improving turnaround times. And it provides an environmental boost by reducing the carbon intensity of concrete.
PREMIACAL is also backed by the world-leading expertise found at the Carmeuse Innovation Center in Pittsburgh, Pennsylvania. Here our team of engineers and scientists are available to be your PREMIACAL Tech Partners, dedicated to your success. With decades of industry experience, combined with technical product expertise, we are dedicated to supporting you to fully realize the performance, economic and environmental benefits of PREMIACAL at your operation.
Please click here to download the article