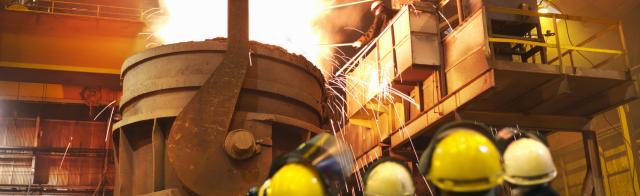
In BOP steelmaking, molten iron from a blast furnace is charged into a refractory-lined furnace, and then oxygen is injected into molten iron at high speeds, resulting in oxidation of carbon and impurities.
High calcium and dolomitic lime is used in several steps throughout this process and results in several enhancements and benefits. In this article, the differences between dolomite lime and high calcium lime will be discussed including their differences and benefits of each.
WHAT IS DOLOMITE LIME (A.K.A. CALCIUM MAGNESIUM CARBONATE)?
Dolomite lime, Dolimitic Lime, or Calcium Magnesium Carbonate is derived from deposits of calcium carbonate combined with magnesium carbonate and contains a high magnesium level. It is a caustic and alkaline crystalline solid.
WHAT IS HIGH CALCIUM LIME?
High calcium lime has a much higher calcium to magnesium ratio with less than 5% of magnesium present. High calcium lime is used in a variety of applications from steelmaking to agriculture, for example high calcium lime is used to raise soils’ pH to improve soil conditions and provide available calcium and magnesium nutrition to your crops.
CALCITIC LIME VS DOLOMITIC LIME
Calcitic Lime and Dolomitic lime can be considered similar products and can have similar applications, such as acting as a fluxing agent in steelmaking. However, they do have distinct differences to be considered such as chemical content and reactivity.
The Benefits of Calcitic Lime
Calcitic lime optimizes chemistry of the slag, removing impurities like sulfur, phosphorus, carbonates, manganese, etc. from the bath to improve steel quality. It also maintains the viscosity of the slag to increase heat yield.
Calcitic Lime’s Limitations
While calcitic lime helps remove the impurities in the bath, by itself it does not offer protection for the refractoried. If used alone an imbalance in the furnace will cause refractory bricks to be worn down overtime increasing operating costs and downtime.
The Benefits of Dolomite Lime
Dolomitic lime is added to the BOF process to increase soluble magnesium oxide in the bath, lowering the tendency of the steelmaking process to steal magnesium from refractories. The magnesium oxide found in dolomitic lime reduces the tendency of slag to dissolve the Magnesium oxide from the furnace refractory. This can prevent melt throughs and protect the refractory
Dolomite Lime’s Limitations
Dolomite lime does not increase yields at the level that calcitic lime would. While the magnesium found in dolomitic lime helps protect the refractory which reduces downtime and increases the lifetime of the furnace, it typically does not contain enough calcium to remove the impurities required for making a clean steel.
HOW ARE HIGH CALCIUM AND DOLOMITIC LIME USED IN STEEL MAKING?
Basic oxygen furnace (BOF) or basic oxygen process (BOP) is a method of primary steelmaking in which carbon-rich molten pig iron is made into steel.
In BOP steelmaking, molten iron from a blast furnace is charged into a refractory-lined furnace, and then oxygen is injected into molten iron at high speeds, resulting in oxidation of carbon and impurities.
High calcium and dolomitic lime is used in several steps throughout this process and results in several enhancements and benefits.
To begin, lime is an important step toward protecting refractories and maintaining basicity, which helps with the removal of sulfur and phosphorus and provides a safer platform to withstand violent reactions in the basic oxygen furnace (BOF).
Many steel plants desulfurize the hot metal externally in torpedo cars or ladles utilizing a flow-aided pulverized lime blend before charging into the BOF. Lime may be used for sulfur and phosphorus removal at this stage. Most importantly, quicklime is typically added to the mixture in the steelmaking furnace after the beginning of the oxygen “blow” where it reacts with impurities (primarily silica and phosphorus) to form a slag which is later removed.
Although steel plants flux with high-calcium quicklime, most of the BOF plants substitute or add 30 to 50 percent dolomitic (higher magnesium) quicklime because experience shows it extends the refractory lining life of the furnaces. While most BOF steel plants use pebble quicklime, the injection systems used in some processes require pulverized quicklime, according to the National Lime Association.
Flux practices involving lime in the BOF have evolved over the years. As with any process, the flux practice employed in the BOP is the result of some basic cost trade-offs. The relative cost of refining needs, iron recovery and refractory savings need to be considered. The typical steelmaking flux practice also is dependent on the starting raw materials.
The ore available to the iron making operation will determine the tramp and trace element load the steelmaking operation will see. The slag chemistry and flux practice of the iron making step is critical for a low-cost operation, and it will strongly determine the practices that will be employed in the basic oxygen steelmaking step.
Any trace element that cannot be removed in refining must be avoided altogether if the load will meet or exceed the steel specification. Examples of this are copper and chrome. This is more of a problem for steelmaking operations that are heavily reliant on scrap metal for most of the metallic charge.
This is an advantage for the integrated shop because most ore-based metallic sources are low in these problem tramp elements that cannot be removed. Another element of concern to the integrated steelmaker is phosphorus because many commercial iron ores available are high in phosphorus. The iron-making step will also recover all the phosphorus charged to the process. The BOP steelmaking step can remove most of the phosphorus with the proper blowing, flux and tapping practice.
CHALLENGES—WHAT THE FUTURE HOLDS
The U.S. and North American steel industry has shown its resiliency to survive the recent economic chaos by adapting through consolidation, addressing technical advancements to improve efficiency, and quality and cost reductions. It has accepted a new paradigm that requires management to be flexible in controlling output when conditions indicate the market is shifting, and it must embrace the concepts of sustainability in a competitive global economy.
The challenges facing a mature BOP industry for the future revolves around these key issues:
- Strategy for sustainability and capital investments
- Energy
- Technological improvements
- Macroeconomics
- Impact of environmental regulations facing steel producers and suppliers of raw materials
Data suggests that in the future, we will see further declines in raw material qualities and increased demand for higher quality levels in steel products. The refining challenge will require re-evaluation of flux practices for controlling such residuals as phosphorus and sulfur.
SUMMARY
The clean steel process starts from the early stage of iron making and the process becomes critical toward the last stages in secondary metallurgical process. High calcium and dolomitic lime selection process plays a critical role in defining productivity, quality and cleanliness from sintering stage to steel melting and finally secondary metallurgy processes. In particular, lime characteristics and process control are key to cleanliness factors such as phosphorus removal and avoiding over oxidation of steel during steel melting in BOF.
Please click here to download the article.